Kobus Van den Berg, General Manager of Underground Production, updates us on the latest progress of De Beers’ Venetia Underground Project during the past year and details the landmark delivery of first production.
MILESTONE DELIVERY
De Beers’ USD$2.3 billion underground expansion of SA’s leading diamond mine, which ceased open pit mining operations in December 2022 after 30 years of production from the Tier 1 asset, represents the biggest single investment in the country’s diamond mining industry for decades.
The highly mechanised underground operation will deliver up to six million tonnes (t) of kimberlite ore per year to produce around four million carats of diamonds annually.
Last year, De Beers celebrated the delivery of first production from underground operations at its Venetia Mine, a highly anticipated milestone and a landmark achievement witnessed by the mining industry.
This significant event marked a new chapter in the history of diamond mining at the Venetia Mine, showcasing the dedication, innovation, and collaborative efforts of all involved.
“The Venetia Mine represents a bold transition from open-pit mining to underground operations, as cemented by the team’s first production blast,” acclaims General Manager of Underground Production, Kobus Van den Berg.
This strategic move was driven by the need to access deeper diamond reserves, opening up new opportunities for the extraction of high-quality gems.
“The increased production will contribute to meeting global diamond demand and solidify the Venetia Mine’s position as a prominent diamond producer,” he adds.
UNDERGROUND TRANSITION
Having delivered first production from its underground operations, the investment in the world-class Venetia Mine will bolster De Beers’ global production in the long term and is an indication of the company’s commitment to SA.
The underground expansion extends the life of the operation by an estimated 25 years, ensuring the continued longevity and sustainability of the Venetia Mine, securing the livelihoods of workers, and contributing to the local economy.
Transitioning to underground mining at the Venetia Mine involved the implementation of advanced mining techniques. For example, the underground mine will use sublevel caving to extract material from its K01 and K02 orebodies.
Initially, the ore will be hauled to the surface using a combination of underground and surface haul trucks. As the operation matures, the hauling systems will transition to an automated truck loop in combination with vertical shafts for steady-state production.
Known for its efficiency and safety, sublevel caving was chosen as the primary mining method, and the journey ahead will likely involve continuous technological advancements.
“The mining industry is constantly evolving and embracing new technologies and innovation which will enhance operational efficiency, safety, and productivity. Automation, data analytics, and advanced monitoring systems will be further integrated to optimise mining operations,” Van den Berg notes.
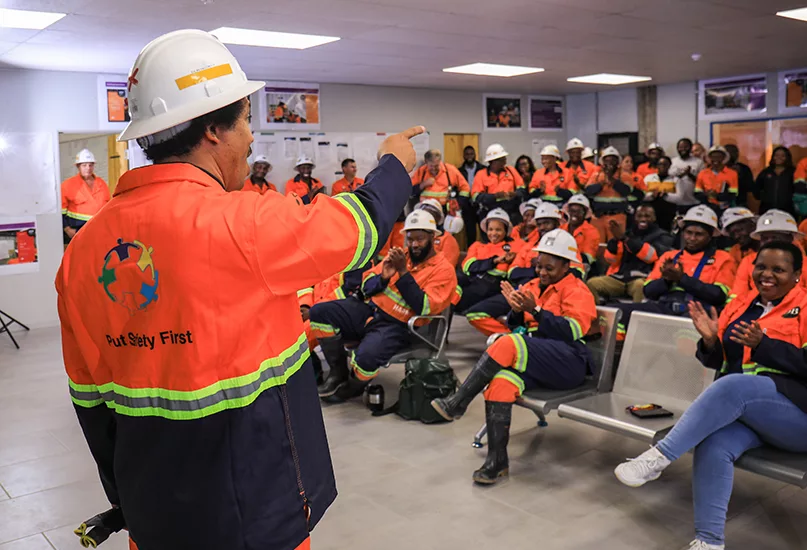
UPSKILLING EMPLOYEES
With these technological advancements and the underground expansion of the Venetia Mine, training has therefore been important to transition De Beers’ employees from open pit to underground mining.
The success of VUP relies heavily on the workforce, and going into an underground operation naturally requires a complete shift in mindset. As a result, De Beers has partnered with a Tier 1 contractor to teach the necessary skillsets.
“This is done through the training and assessment of our employees. In this way, we will ensure that no one is left behind and they have the necessary skills to take VUP further,” says Van den Berg.
“Upskilling our team to operate a mine of the future remains key. We are prioritising the training of long drill operators, who are crucial to advancing VUP, and trackless mobile machine operators following the first production in June 2023.”
To date, more than 30 000 interventions for both new and existing employees have been completed since the USD$10.5 million Venetia Mine training centre was commissioned in June 2021. This was a key component of its operational readiness framework to enhance the transformation of people, processes, and systems for the successful transition from open pit to underground mining.
Training covers areas such as health and safety, the operation of underground equipment, and technical aspects, including geology. It also involves training for ventilation, which is key for underground operations, as well as sophisticated equipment such as winders.
Early warning systems training is also undertaken to ensure that mine workers understand the meaning of various alarms for safety purposes.
As De Beers is building an underground mine that will eventually be autonomous, skilled personnel are therefore required for this ambitious technological development.
“People will still be responsible for operating mining equipment, but will do so remotely, removed from any potential danger underground,” confirms Van den Berg.
As a follow-up to the training which employees receive at the centre, De Beers has partnered with Tier 1 mining contractor, Redpath, to further enhance the skills of its operators on key mechanised equipment and ensure safety and performance levels meet international mining standards.
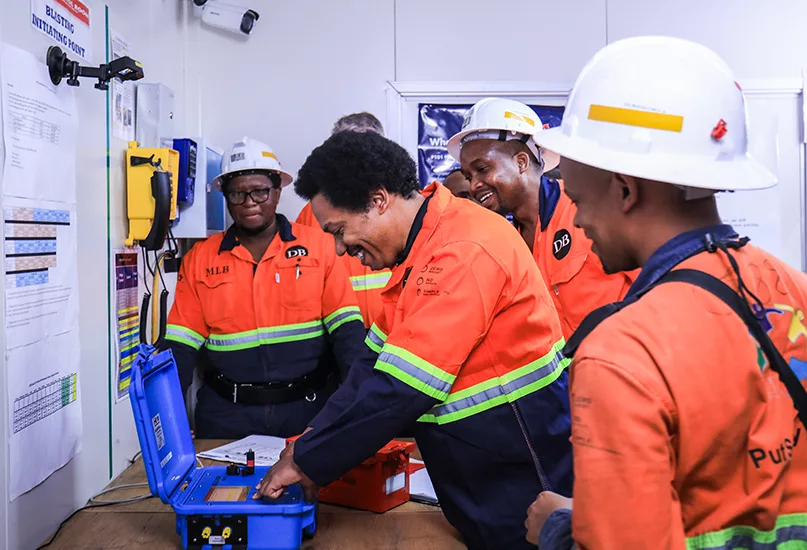
FULLY AUTONOMOUS MINE
In order to create a fully autonomous mine, the company’s digital transformation journey continued to progress in 2023 and is an integral part of the underground expansion.
De Beers’ objective is to have a number of autonomous mining systems performing multiple processes by 2027. The introduction of these systems is now beginning, with a ramp-up process occurring over the next four years.
The technologies that De Beers is implementing, some of which are under development, will be gradually phased in.
“Automation at VUP will be applied in a phased approach, then gradually introduced with the necessary training in the operation and support of these technologies,” Van den Berg divulges.
VUP has partnered with Sandvik Mining and Rock Solutions (Sandvik), who manufactures the iSeries range of intelligent automated mining machines, which can be operated underground within access-controlled safety zones or from a control room on the surface.
Sandvik has delivered a 34-strong fleet made up of load haul dump (LHD) machines, articulated dump trucks (ADTs), twin-boom drill rigs, roof bolters, cable bolters, and production long hole drills.
“These iSeries machines include 17 and 21 t payload LH517i and LH621i LHDs, 51 t payload TH551i ADTs, DS412i roof bolters, DS422i cable bolters, DL422i production drills, and DD422i face drills,” shares Van den Berg.
“Automation at VUP will be applied in a phased approach, then gradually be introduced with the necessary training in the operation and support of these technologies”
Kobus Van den Berg, General Manager of Underground Production, Venetia Underground Project
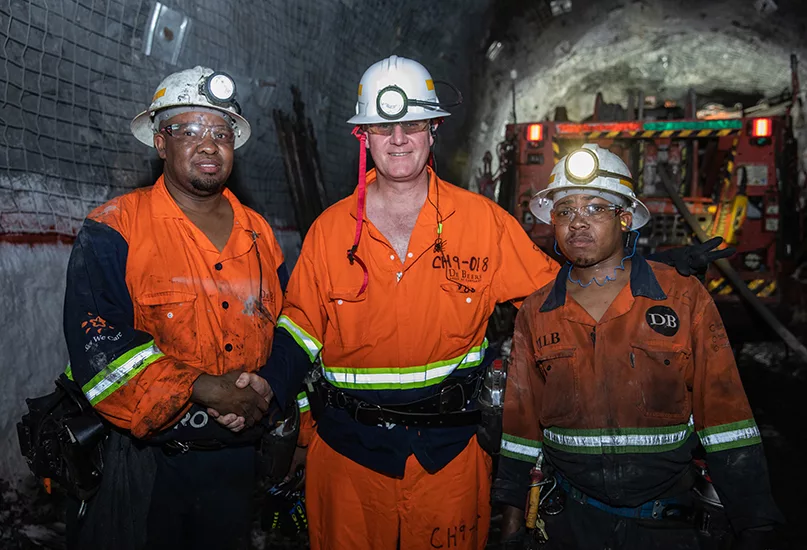
