As proud pioneers of secondary metals manufacturing, UNICA Iron and Steel is successfully forging a path in South Africa. Managing Director, Mohammed Asif Qasim, tells us more about the industry.
SETTING A SOLID STANDARD
Established in 2007, UNICA Iron and Steel (UNICA) is the first in South Africa (SA) to feature a fully integrated mini-steel plant that produces light to medium structural steel.
“We are growing with the pace of demand, and our market share increases daily. We are currently installing a new melting furnace to increase our capacity from 120,000 tonnes per annum (tpa) to 240,000 tpa,” opens Mohammed Asif Qasim, Managing Director of UNICA.
Qasim began his career as an entrepreneur and retail shop owner. He developed an interest in the manufacturing industry as an industrialist in 1998 when UNICA Plastics, as it was then known, started in Pretoria.
Subsequently, a steel fabrication shop was incepted in 2000, and following that, the company evolved into UNICA Iron and Steel, where Qasim became the Managing Director, co-Founder, and a shareholder.
Alongside the melting furnace, Qasim proudly tells us of other projects in the pipeline for UNICA. For example, in an effort to optimise its production capacity, the company added argon oxygen decarburisation (AOD) and oxygen plants to its production processes.
“We are installing two oxygen plants and one AOD unit, which will allow us to improve our quality further and supply different market sectors,” Qasim tells us.
AOD is a chemical process where oxygen is introduced in a vessel to create an exothermic reaction, hence, UNICA installed oxygen plants alongside it. As a result, the plant produces oxygen and nitrogen necessary for decarburising and refining the steel.
“We have invested over R450 million since the COVID-19 pandemic and are continuing to do so. Once all the expansions are completed, we may be at the level of R550 million,” Qasim notes.
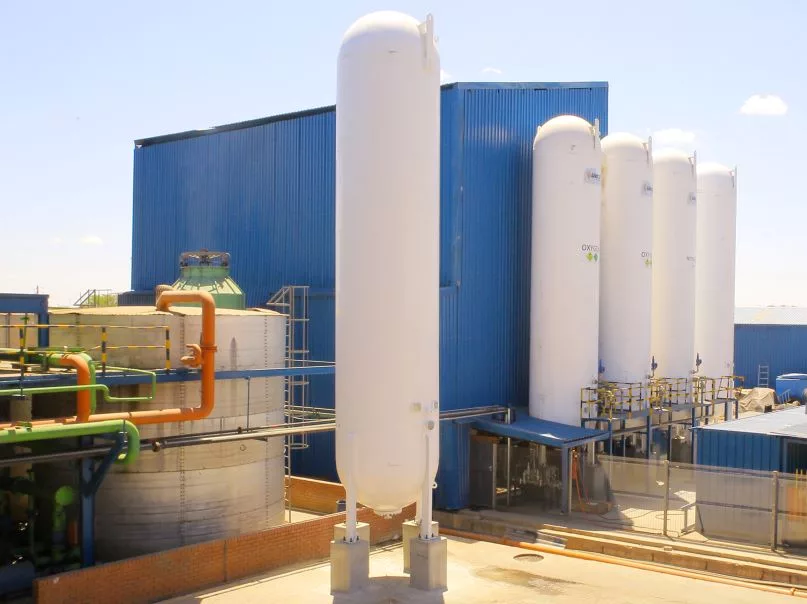
PROCESSES AND PLANTS
The company uses processed scrap as a raw material to produce steel using an induction furnace, in a process known as secondary steel making. The resultant billets are then processed in the rolling mills to produce light to medium steel sections such as angle iron, round bars, and window sections.
“Focusing on this niche, UNICA has managed to grow its share substantially and has become a benchmark operation for many who have followed its success,” Qasim reveals.
“The company is the first 100 percent Bureau of Energy Efficiency (BEE) rated metal waste recycle plant in the small and medium-sized enterprises (SME) space.”
Indeed, UNICA has much to celebrate, and its success is partly down to the 900 people it employs from the rural Hammanskraal area in Gauteng Province. The workforce operates in rolling mills to produce over 100 different sections from billets created in an induction furnace and castes in a continuous caster.
“When the plant was established, it was able to produce only 12,000 tpa, whereas in the space of 14 years, it has already reached the levels of 15,000 tpa and is expanding further, so we are hoping to reach up to 24,000 tpa by Q3 in 2024.
“Next year, the process involving melting scrap to liquid metal and casting it to billets, which are then reheated and rolled from light to medium,” Qasim informs us.
Before 2007, only six major steel-making plants existed in the country, which were dominating the sector, particularly since there were only two major plants in the long products market.
“That is where we saw a gap; therefore, we decided to adopt the Asian mini steel plant. Our success followed, with five or six more plants established after us,” continues Qasim.
“Focusing on this niche, UNICA has managed to grow its share substantially and has become a benchmark operation for many who have followed its success”
Mohammed Asif Qasim, Managing Director, UNICA Iron and Steel
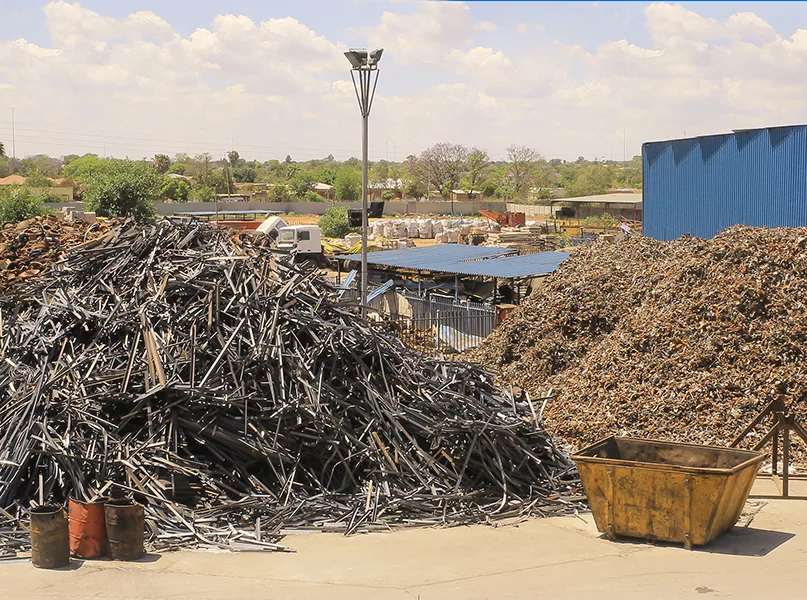
STRENGTHENING COMMUNITIES
“One of the reasons that UNICA is growing and successfully capturing the market is due to our dedicated, motivated, and well-trained workforce. Our experienced executive, senior, middle, and junior management in particular are key reasons for our prosperity,” Qasim sets out.
As UNICA is a first-of-its-kind project in SA, most of its staff had no first-hand experience in the demands of secondary steel manufacturing. To address this, the company’s HR department provides on-the-job training.
“We also provide ample training and opportunities for career growth by encouraging our employees to work smart,” he adds.
Over the years, the company has consistently improved staff conditions, and now it is the highest-paying employer in the country. Furthermore, it distributes annual bonuses, long service awards, and production incentives. Employees of the month and year are just some of the initiatives that make UNICA the workplace of choice.
As part of UNICA’s mission, vision, and values, it is also deeply committed to making a difference in the community through its corporate social responsibility (CSR) programmes.
“We provide economic and equal opportunities to our immediate community by offering direct jobs to citizens in surrounding areas. We ensure that we also extend a helping hand to widows and orphans.”
Other programmes include rehabilitating drug users and educating communities on drug abuse as well as the prevention of violence against women.
“Sporting activities are also one of our key principles. As such, we sponsor local sports events and kits for teams,” acknowledges Qasim.
As corporate citizens, UNICA believes its impact on the local communities and surrounding environment must be positive. To that end, the company encourages a culture of care, supporting multiple projects to uplift the disadvantaged and assist those less fortunate.
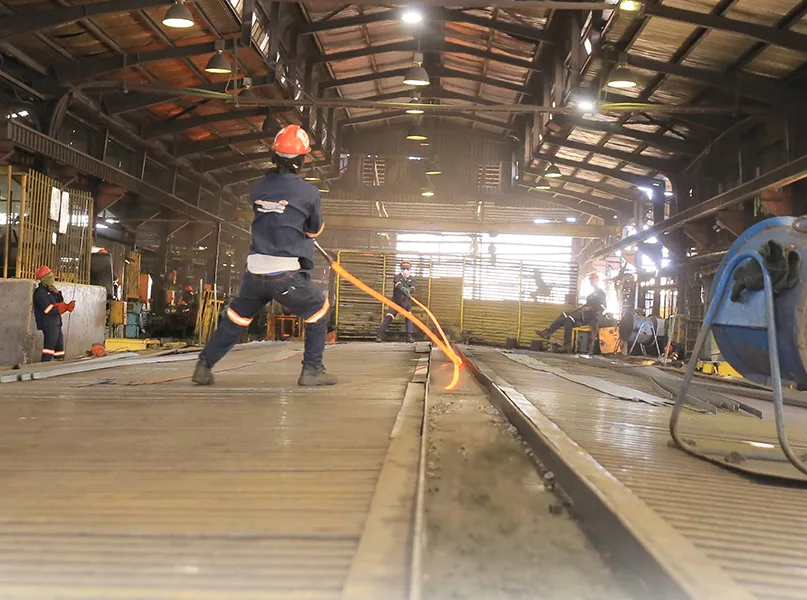
UNICA UPGRADES
As the plant is the first of its kind in SA, it is unique in its totality.
“We have adapted many different methods in billet-making and rolling processes to innovate our profile. We produce and offer better commercial benefits to our market; for example, we are the first in the country to master and successfully produce light angles of 2 millimetres (mm) gauges.
“Similarly, we have produced a special window section, which is light in weight but still does not lose strength due to its innovative design,” Qasim enthuses.
The steel industry is one sector that the government has focused on, especially since the COVID-19 pandemic. More aggressive steps have been taken by the current administration, having who has developed a master plan for the industry, encouraging even greater growth for UNICA.
Moreover, the localisation drive and protection of regional products has played an important role in UNICA’s growth after the devastation caused by the COVID-19 pandemic.
“During 2020, we completed a new rolling mill, which has allowed us to expand our billet-making capabilities. Subsequently, the second expansion since the COVID-19 pandemic is underway. This growth is a direct result of our continuous hard work, R&D, and customer-orientated attitude, by providing clients with flexibility and easy access to our ordering and delivery systems,” he details.
All expansions are carried out with calculations and market surveys, demonstrating how UNICA sets realistic targets and achieves them to the maximum extent.
“Our current goal is to cross the 24,000-tonne figure by the end of 2024. We are well on course, and I believe we will get there,” Qasim closes.
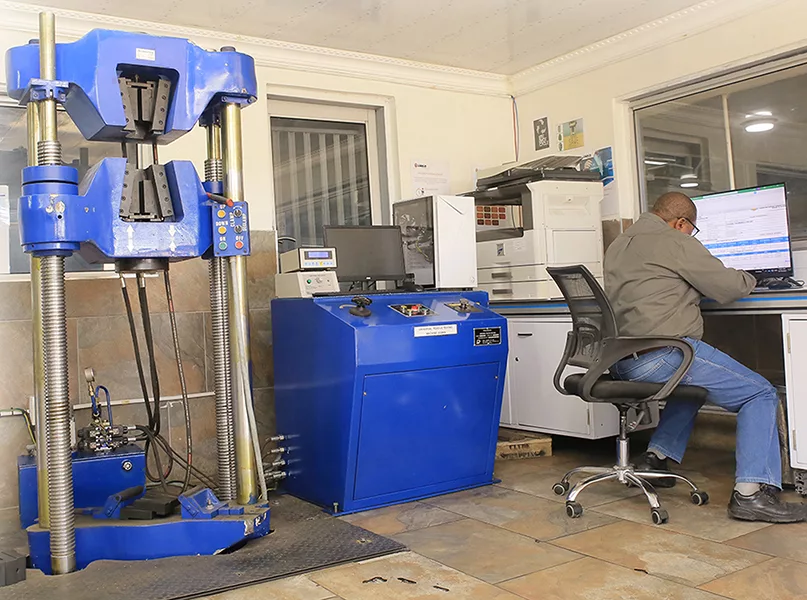