Comprehensively supporting customers, Sulzer South Africa is dedicated to improving pumping processes, operational reliability, and the high performance of industrial rotating machinery. We discuss all this and more with Managing Director, Henry Craukamp.
CELEBRATING A CENTURY OF HERITAGE
There is often a tendency to label Africa as one market or industry, but it’s important to remember that the continent is made up of 54 distinct nations, each with their own unique opportunities and challenges.
Several noteworthy trends are shaping the current landscape, as despite the enduring challenges posed by the COVID-19 pandemic, many African companies are steadfastly maintaining their focus on pivotal trends, including digitalisation and sustainability.
It is no secret that Africa is simultaneously experiencing an increase in urbanisation, leading to an upturn in the need for water and electricity. The global requirement for natural resources also continues to boost investments in the mining industry, as the demand for raw materials is still a powerful factor in continued investments in the vast African mining sector. Meanwhile, across a plethora of African industries, the intense competition for talent acquisition remains an ongoing and pressing concern for businesses.
Expertly navigating these numerous challenges is Sulzer South Africa (Sulzer), established in 1922, who has intricately built a rich company legacy rooted in the region’s industrial growth.
“Our evolution from diesel engines and boilers to comprehensive electrical services marked the early stages of our diverse portfolio,” introduces Henry Craukamp, Managing Director of Sulzer.
“Over the years, we have expanded our offerings to include solutions beyond pumps, catering to industries such as water treatment, chemical solutions, transportation, food processing, and power generation,” he expands.
Craukamp is a seasoned business leader with a wealth of experience in various aspects of the industrial and engineering sectors. As of 2022, he serves as the Managing Director and Compliance and Information Officer at Sulzer, where he oversees the entire business, assuming responsibility for sales and operations within the region.
With approximately 300 employees, the company’s operational region currently serves customers in 10 countries from within South Africa, based out of two major service locations, Johannesburg and Welkom. Sulzer’s overarching mission as a full-service provider is to adapt continuously to meet the country’s evolving needs.
Throughout Sulzer’s history in South Africa, it has accumulated extensive experience in navigating the complexities of investing, divesting, and reinvesting in a variety of countries and industries.
“Our experience has enabled us to adapt and evolve as the landscape changes, and we find that difficulties like these are truly inspiring,” Craukamp tells us.
“By transforming challenges into opportunities, we can provide solutions that directly meet the specific needs of our customers. At Sulzer, we are more than just a product supplier; we aspire to be true partners in delivering substantial value to our customers.”
“Our evolution from diesel engines and boilers to comprehensive electrical services marked the early stages of our diverse portfolio”
Henry Craukamp, Managing Director, Sulzer South Africa
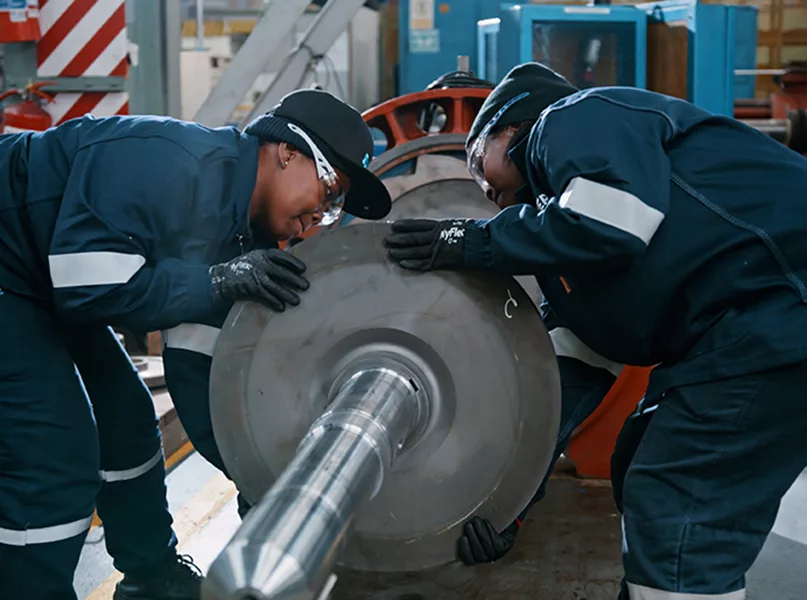
A HISTORY OF EXCELLENCE
The roots of Sulzer’s history lie in the development of a range of pumps used in diverse applications where fluids are treated, pumped, or mixed.
“We can stand out from the competition in this market because of our facilities, manufacturing and engineering capabilities, and the level of service we provide our customers,” Craukamp acclaims.
A great example of Sulzer’s engineering capabilities is its ability to design equipment for a variety of industries and applications.
“We have crafted a team of seven engineers, with backgrounds in turbine and hydrodynamic design, who are not only involved in local projects but also in global R&D efforts,” he elaborates.
Because of this, Sulzer is more competitive than other pump manufacturers with centralised engineering activities. Moreover, the company has developed reverse engineering capabilities, so it can provide solutions for mechanical rotating equipment, high-speed gearboxes, hydrodynamic couplings, and electromechanical systems. In addition, customers can also benefit from Sulzer’s global network of expertise and know-how.
With specialised requirements and a limited number of experienced service engineers in the industry, Sulzer values experience and knowledge. Throughout the organisation, the company invests a lot of time and effort in training and developing its employees.
“With one engineer working with us for over 25 years, we have a seasoned, experienced engineering team and value their contributions highly.”
With respect to Sulzer’s specialised capabilities, it boasts two service centres in Elandsfontein and Welkom that provide pump, rotating equipment, and electromechanical services. Additionally, the company offers in-house full-performance testing for pump systems, allowing the customer to feel confident when installing the equipment and reduce commissioning time.
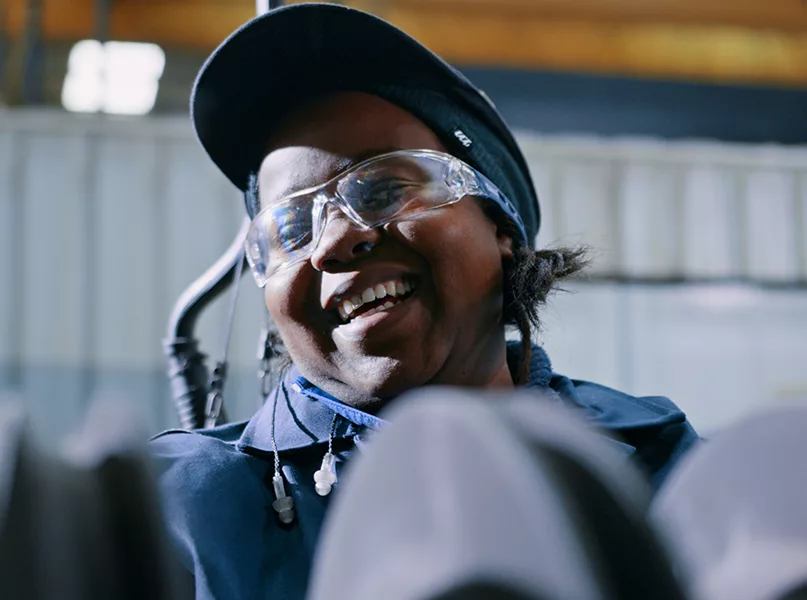
EXCEPTIONAL SOLUTIONS AND SERVICE
Sulzer has played a pivotal role over the last century by delivering exceptional solutions through its comprehensive engineering expertise, industry-specific product range, and customer-centric services.
“While we are often recognised as the preferred pump company, our offerings go far beyond pumps and pump-related services. Our journey in South Africa traces back to the early 1900s when we were involved with diesel engines and boilers, preceding our formal establishment in 1922,” Craukamp shares.
The company then seamlessly diversified into electrical services in 1925, before opening a pump reconditioning service centre in Jeppestown in 1936 to cater to the thriving gold industry of the 1940s.
“To further support South Africa’s growth, we inaugurated a pump factory in 1951. During this period, we played a vital role in advancing the power, mining, and water sectors,” he adds.
However, as the late 1960s approached, Sulzer anticipated a decline in demand for mine dewatering pumps, prompting a shift towards the power generation market and the increasing public need for water supply.
In 1976, the company established a purpose-built pump manufacturing facility in Elandsfontein, which not only produced world-class pumps but also provided a comprehensive range of spare parts. This marked the inception of Sulzer’s journey as a combined supplier of new pumping assets and a service provider for rotating equipment.
Furthermore, in 1979, a dedicated workshop for rotating equipment was introduced, aligning with the aging equipment in South Africa, proving to be a prudent move for both the company and its customers. Collaborations with original equipment manufacturers (OEMs) to manufacture approved spare parts further solidified Sulzer’s offering.
“While the 1980s witnessed the era of big hair and power dressing across the world, Sulzer was busy evolving into a leading independent service provider (ISP) in South Africa.”
This impressive transformation was facilitated by the establishment of a new engineering department in 1984, and by the end of the decade, Sulzer had become a fully-fledged ISP for rotating equipment for nearly any brand.
Staying true to its heritage of adapting to customer needs, in 2023, Sulzer opened a state-of-the-art electromechanical services facility in Elandsfontein. This facility aligns with the company’s commitment to not only enhance its customers’ pump performance, but also optimise the entire associated drivetrain.
More from Africa Outlook
The facility further bolsters Sulzer’s capabilities in refurbishing motors, gearboxes, and generators, offering customers in South Africa a comprehensive one-stop shop for their rotating equipment needs. Additionally, when necessary, customers can access Sulzer’s global network of over 100 service centres for comprehensive maintenance and repair works.
“By transforming challenges into opportunities, we can provide solutions that directly meet the specific needs of our customers”
Henry Craukamp, Managing Director, Sulzer South Africa
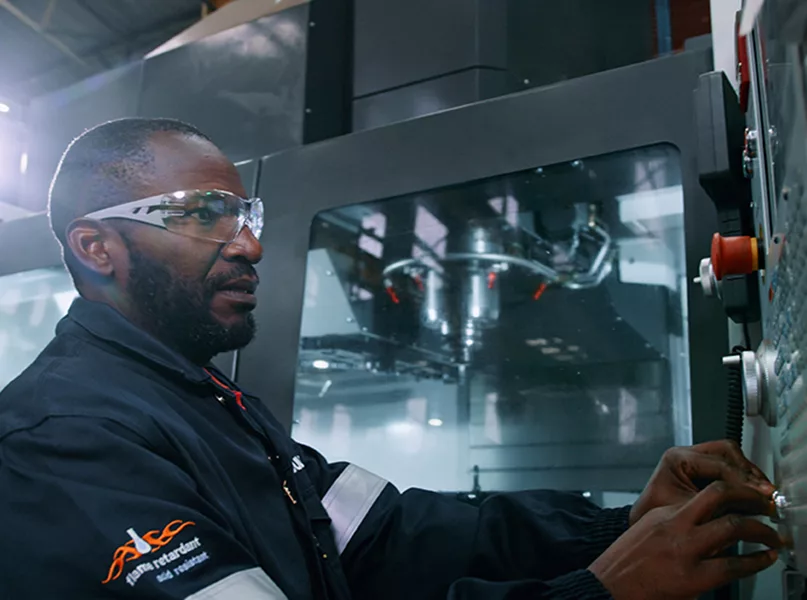
CSR PROJECTS
Sulzer not only cares for its customers, but also for the communities where it operates.
“This is part of our identity, our vision, and deeply rooted in our employees’ DNA. Our sense of care binds us together even more,” Craukamp exudes.
In 2021, the company introduced the Sulzer Scholarship for Women in Science and Engineering. This scholarship is targeted at female students pursuing degrees in engineering, technology, and science, with the ultimate goal of increasing female participation in the engineering industry.
As part of Sulzer’s commitment to the communities in which it operates, the company is actively collaborating with universities in South Africa to establish and promote these scholarships, reflecting its presence and business needs in the region.
Sulzer further demonstrates its commitment to education by providing financial support to 10 students from Volksrus Primary School on an annual basis.
“Furthermore, in 2023, we embarked on a two-year restoration project for Primrose Primary School. This project not only aims to provide students with a school to take pride in, but also to create a safe and conducive learning environment, especially for students from the local informal settlement,” he adds.
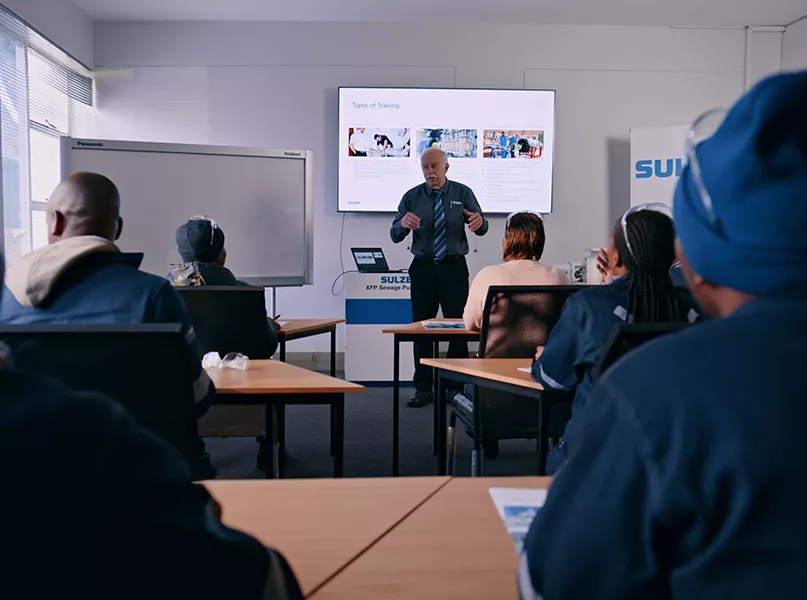
STRATEGISING FOR A BRIGHT FUTURE
Sulzer aims to be a responsible corporate citizen and endeavours to harness the power of fluid engineering to make life better, safer, and more sustainable.
“Our sustainability strategy is composed of three pillars – minimising our carbon footprint, enabling a low-carbon society, and engaging our employees and communities to build a more inclusive and sustainable future,” Craukamp offers.
The three pillars are supported by Sulzer’s commitment to the principles of good corporate governance, which ensure a sound balance of power and support the company in creating sustainable value for its various stakeholders.
Sulzer actively engages with its customers to address pump-related challenges, such as failures and evolving specification issues. Sulzer is also heavily investing in R&D for leading engineering solutions to address these issues.
“For example, we are working on utilising additive manufacturing for pump repairs and retrofits. This approach underscores our commitment to environmentally-responsible practices, reducing the need for equipment disposal or extensive remanufacturing, thus aligning with our dedication to minimising our carbon footprint and advancing a low-carbon society.”
Looking ahead, Sulzer’s key priorities include further enhancing its engineering capabilities, expanding its local footprint, and investing in advanced technologies.
“We aim to position Sulzer as a leader in innovative solutions, ensuring our services align with evolving industry needs. Our focus on customer satisfaction, sustainability, and continuous improvement drives our strategic vision,” Craukamp sets out.
“While specific targets are confidential, our overarching goal is to achieve sustainable growth, offer unparalleled customer experiences, and contribute meaningfully to the communities and industries we serve,” he excites.
To summarise, Sulzer continues to expertly provide a comprehensive range of solutions to its customers.
It is the company’s robust engineering capabilities and facilities in close proximity to its customers that set it apart from various competitors. Investing in continuous learning and development for its employees allows Sulzer to guarantee its services meet the highest standards, and will ensure that the company remains a leading full-service provider in the market.
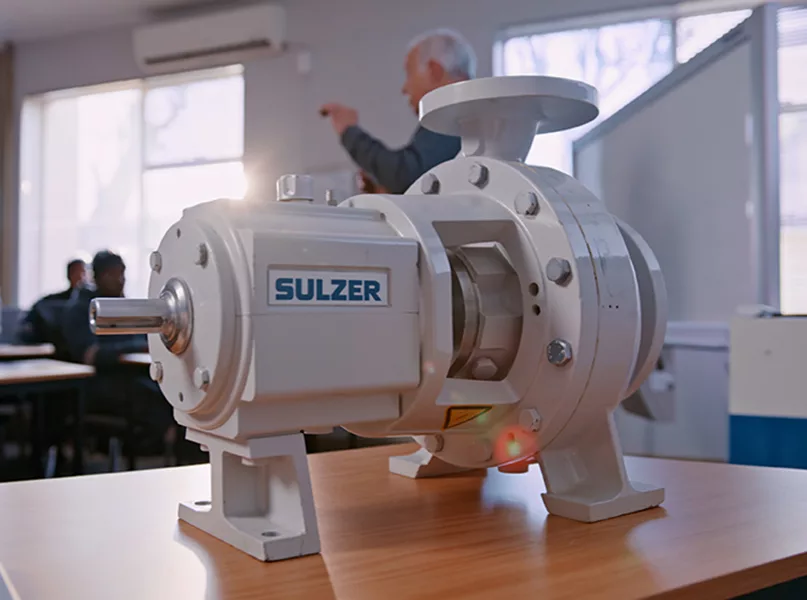